System development & validation
Development and validation
of thermal management systems
and their components
During system development, we combine the individual components of the refrigerant and cooling water circuits to create an optimally harmonised overall system. Using realistic test bench tests, we analyse and evaluate the interaction of all components and optimise the thermal management system specifically for performance, efficiency, functionality and durability. And we do this for a wide variety of system designs and functionalities – from a simple refrigeration circuit with evaporator and chiller to a complex heat pump system with different heat sources and sinks. All typical automotive refrigerants such as R134a, R1234yf, R744 and R290 can be used, depending on the wishes and requirements of our customers. We have state-of-the-art thermal management test benches, including the necessary measurement technology and sensors, to test and validate both individual components and complete systems in their entirety. Through structured test procedures, we ensure that each system works reliably and fulfils the high requirements in real-life use.
System development & validation
Our thermal management system test benches are not only used for the development and validation of refrigerant and coolant circuits themselves, but also for the development and validation of associated operating strategies and control functions. In an initial implementation step – known as function prototyping – the desired system functions are realized using model-based development tools such as MATLAB Simulink. These functions are made operational on the real system setup at the test bench using rapid prototyping control units. The corresponding function control module is then iteratively optimized and refined within the full system context until the actual system behavior matches the expected function performance. Once this alignment is achieved, the “proof of concept” for the respective control function is considered complete. Based on the implemented function, a corresponding functional specification can be derived and formally documented, forming the foundation for subsequent software development.The real system setup at the test bench also provides a valuable platform for initial calibration, the development and validation of diagnostic functions, and durability testing.
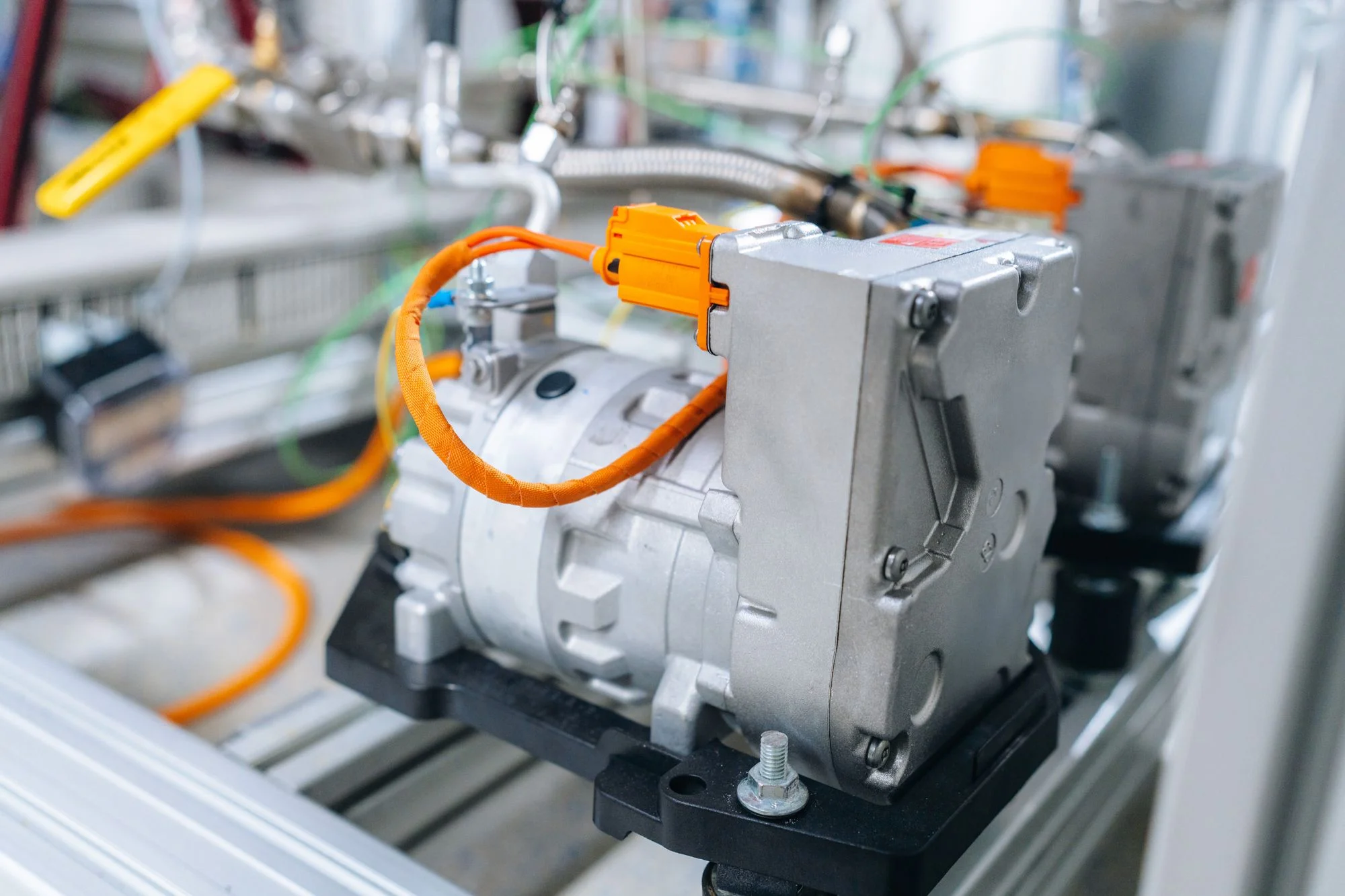
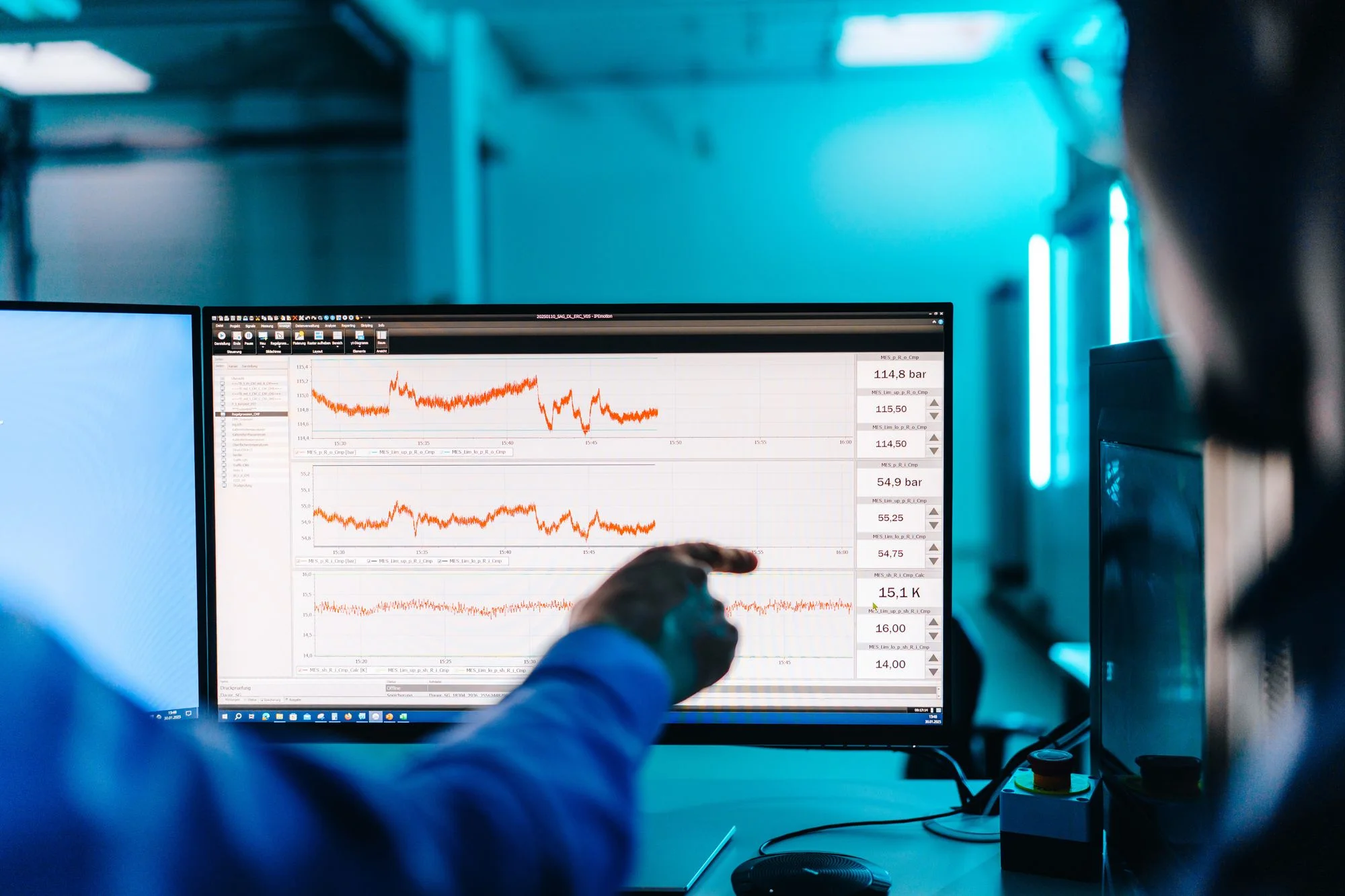
Complex and interconnected refrigerant and cooling water circuits
In hybrid or battery electric vehicles, the high-voltage batteries used are usually cooled via a water circuit. This cooling water circuit is coupled to the refrigerant circuit by the so-called chiller and can therefore be actively cooled.
Networked system controlled systems
The coupling of the refrigerant circuit with the cooling water circuit also leads to a networking of these two control systems and brings with it a corresponding cross-influence of these two fluid circuits.
Extended range of functions
An efficient and intelligent heating, cooling and air conditioning system is essential to optimise the range of the vehicles. One way of doing this is to implement a heat pump function.
Holistic development approach
We pursue a holistic development approach and utilise the synergies from our system and function control expertise to bridge the gap between system and function.
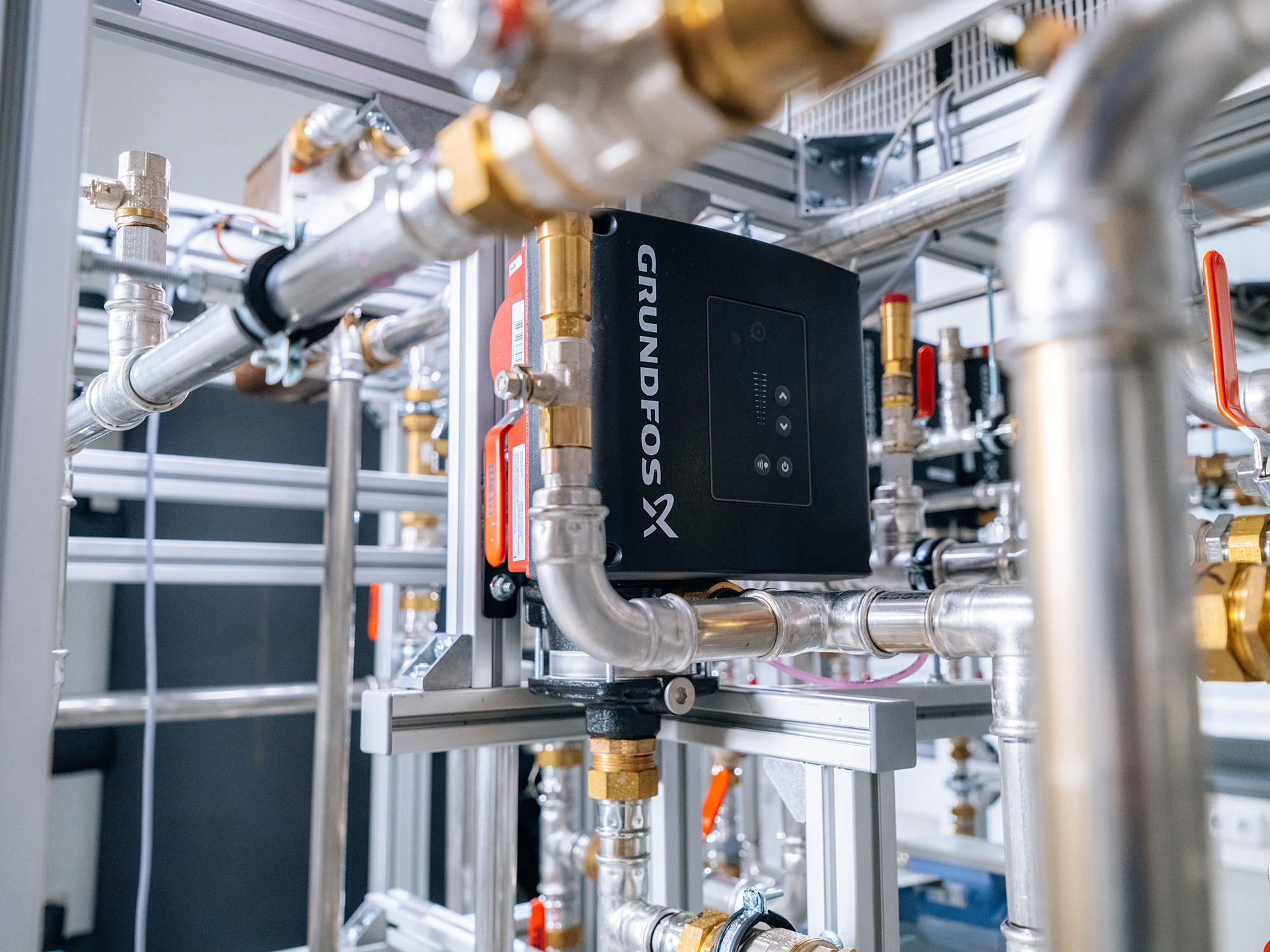
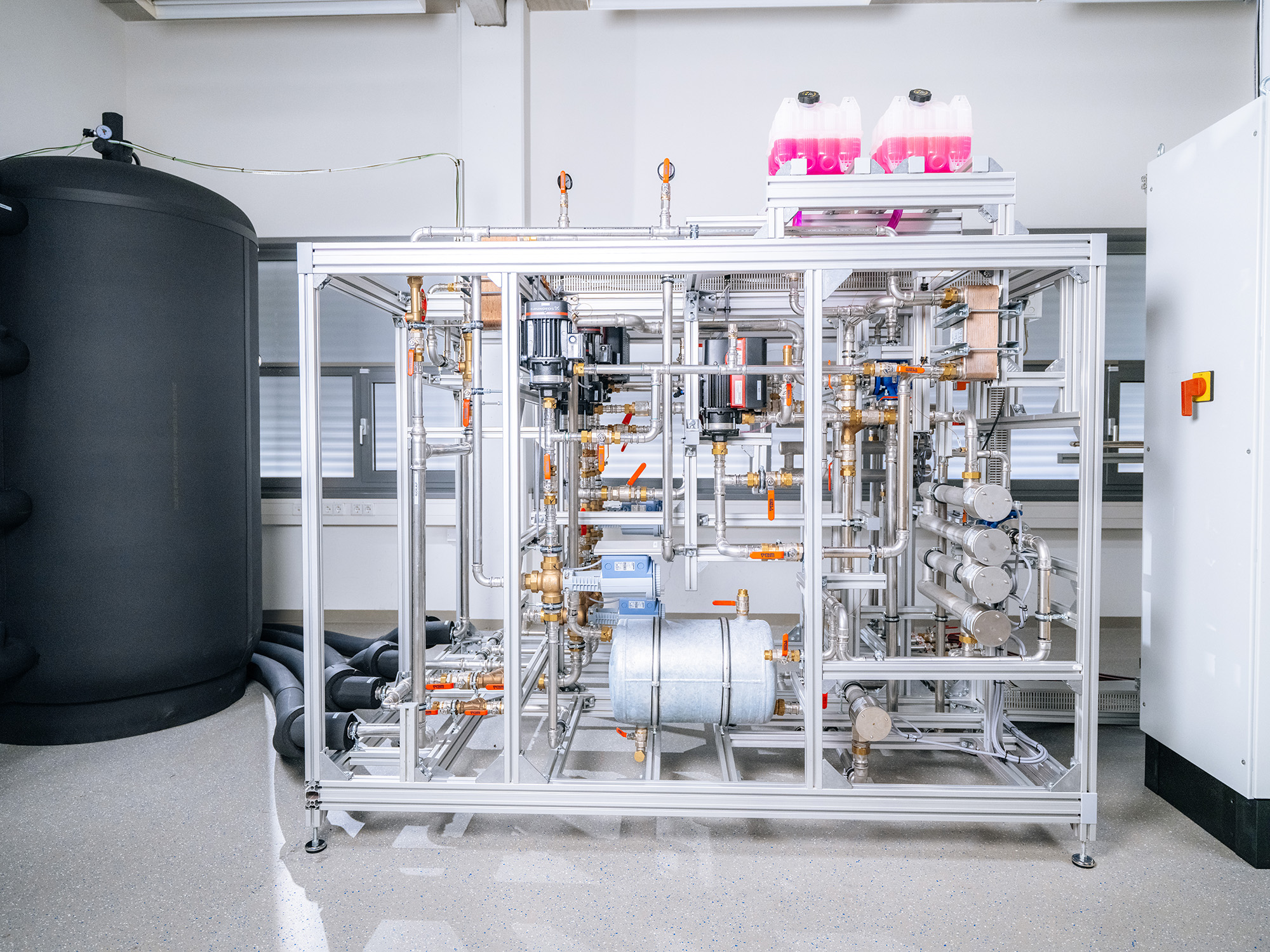
System tests under real environmental conditions with state-of-the-art test benches
On the thermal management system test bench, a wide range of environmental conditions can be customised for carrying out system tests. From arctic cold to tropical heat – on up to three independent air sections and cooling water simulation modules.
Determining the optimum refrigerant charge
The refrigerant circuit requires a defined refrigerant charge for all operating states in order to work optimally at all times. This is why one of the first project goals is to harmonise a standard charge.
Coordination of oil management
In addition to the correct refrigerant charge, effective oil management is one of the key requirements for achieving the target values for system durability, performance and efficiency.
Performance and efficiency measurements
We equip the refrigerant and cooling water circuit with the necessary measurement technology and sensors according to customer specifications in order to be able to analyse the system’s performance and efficiency at any time.